Step-by-step guide to the Thermoforming process.
Thermoforming is an efficient and versatile plastic manufacturing process that transforms flat plastic sheets into durable, custom-molded components. This process is commonly used to produce parts for a wide range of industries, including automotive, medical, agricultural, and consumer products. At Medallion Plastics, we use advanced thermoforming techniques to create high-quality plastic components that meet your specific requirements. Below is an overview of the key steps involved in the thermoforming process.
1. Heating
The process begins by heating a plastic sheet until it becomes flexible and malleable. The sheet is placed into a specialized oven where it is uniformly heated to the optimal temperature, specific to the type of plastic being used. This careful heating ensures the material reaches the ideal pliability without degrading its properties.
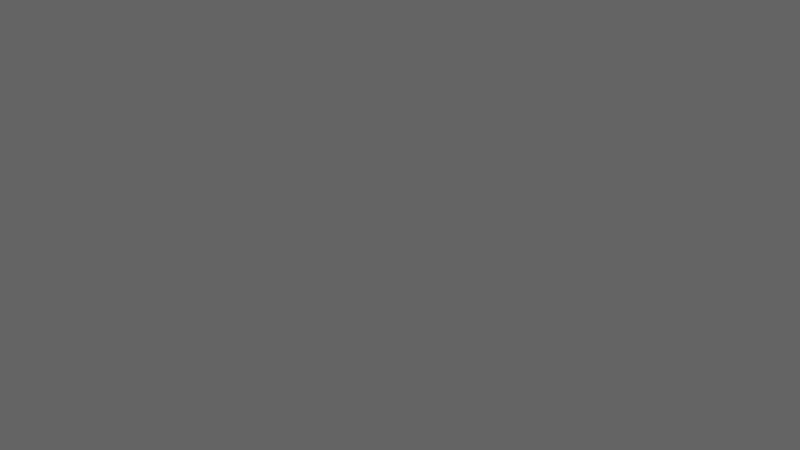
2. Forming
Once the plastic sheet is heated, it moves to the forming stage. The malleable sheet is positioned over a custom-designed mold. Using vacuum, pressure, or mechanical forming techniques, the sheet is shaped to the exact contours of the mold. This step is critical as it defines the final shape and features of the part. Our advanced equipment allows for intricate designs and precise details, accommodating a wide range of product specifications.
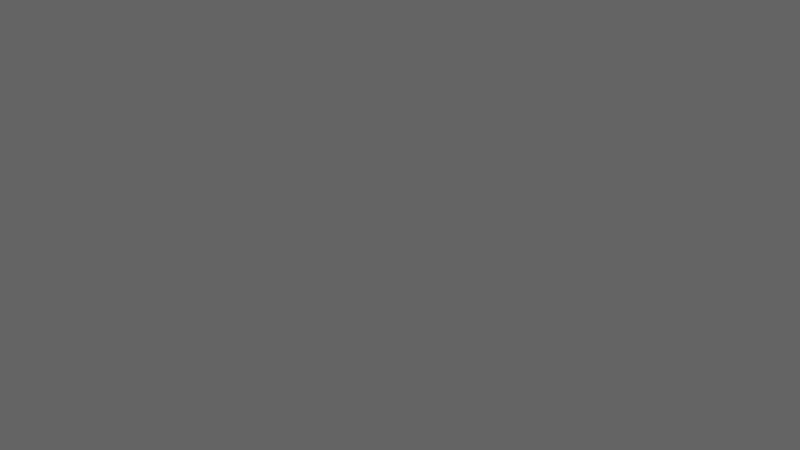
3. Cooling
After forming, the plastic needs to cool while retaining the shape of the mold. Cooling solidifies the material, locking in the shape and ensuring structural integrity. The part remains on the mold during this phase, and cooling can be accelerated using fans or a cooling system to maintain efficiency without compromising quality.
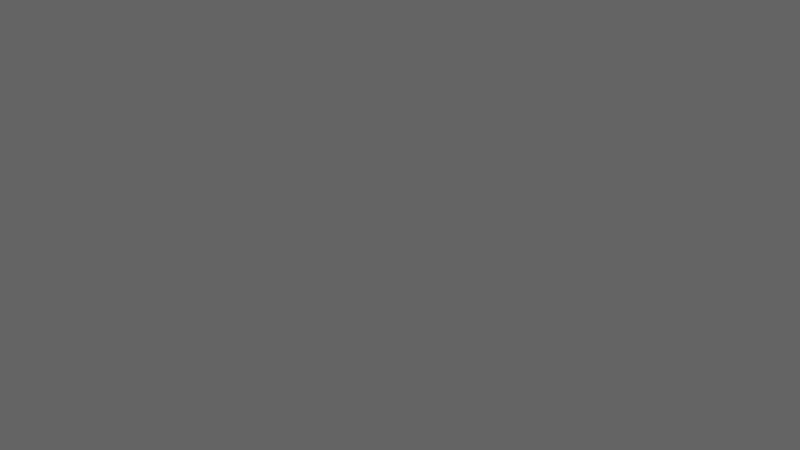
4. Trimming
Once cooled and solidified, the formed plastic part undergoes trimming to remove any excess material. Precision trimming is essential for achieving clean edges and exact dimensions. We utilize techniques such as CNC routing, die cutting, or hand trimming, depending on the complexity and requirements of the part. This step ensures the final product meets the specified tolerances and aesthetic standards.
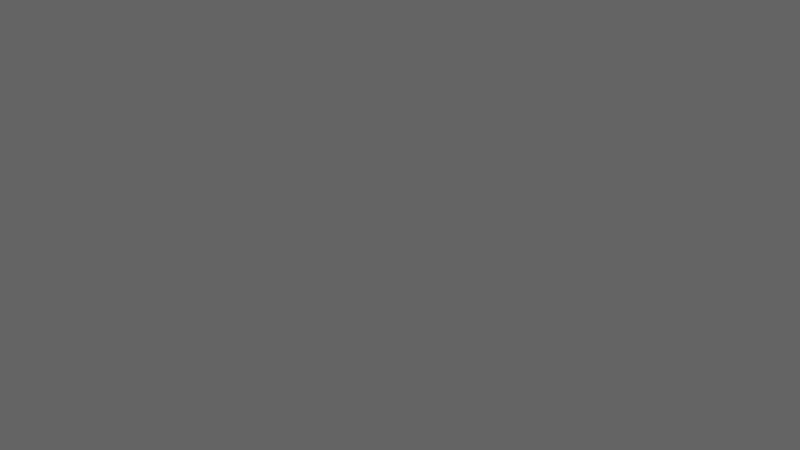
5. Finishing
The final stage is finishing, where additional processes are applied to meet specific product requirements. This may include:
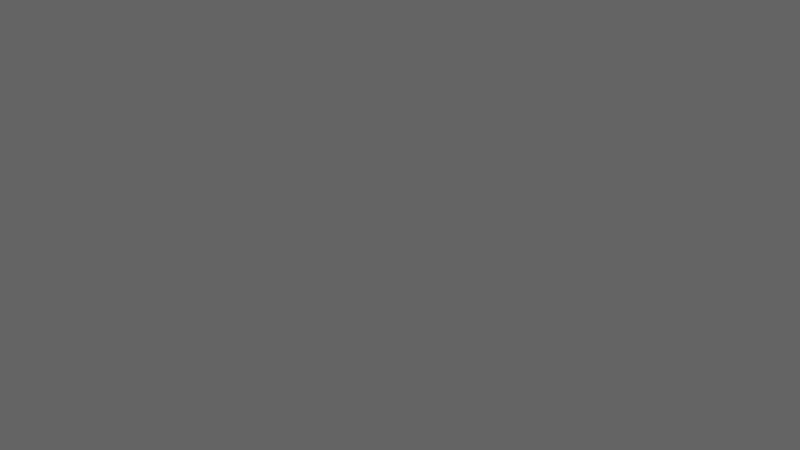
Our commitment to quality at every step ensures that the finished product is ready for immediate use or further integration into your production line.