Unlocking the benefits of Thermoforming for your business.
Thermoforming offers numerous advantages that make it an ideal choice for manufacturing high-quality plastic components across various industries. Here are some key benefits of the thermoforming process:
Cost-Effective Production
Thermoforming requires lower tooling and production costs compared to other molding methods like injection molding. This cost efficiency makes it suitable for both small and large production runs, allowing businesses to manufacture products economically without sacrificing quality.
Design Flexibility
The process allows for the creation of complex shapes, deep draws, and intricate details. Thermoforming can accommodate large parts with unique geometries, giving designers the freedom to innovate and customize products to specific requirements.
Quick Turnaround Time
With faster setup and production times, thermoforming accelerates the manufacturing process. This efficiency reduces time-to-market for new products, which is crucial in competitive industries that demand rapid prototyping and swift design adjustments.
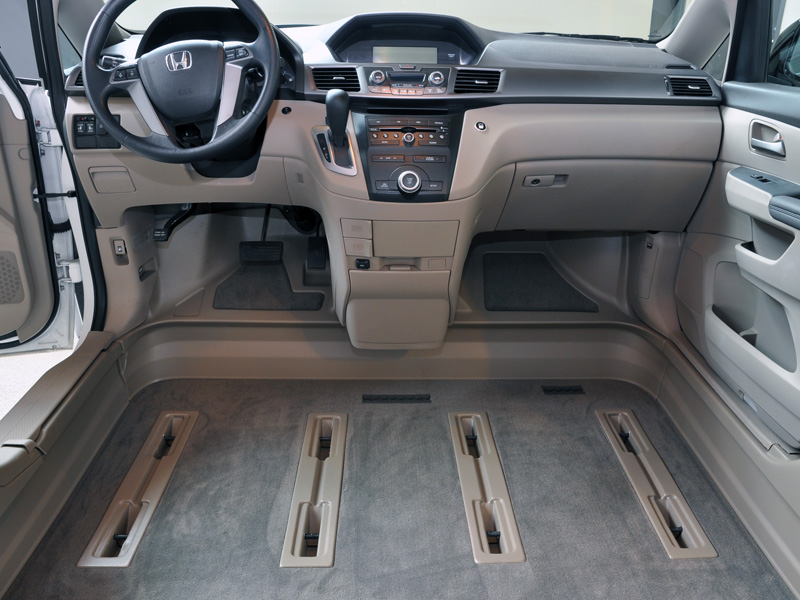
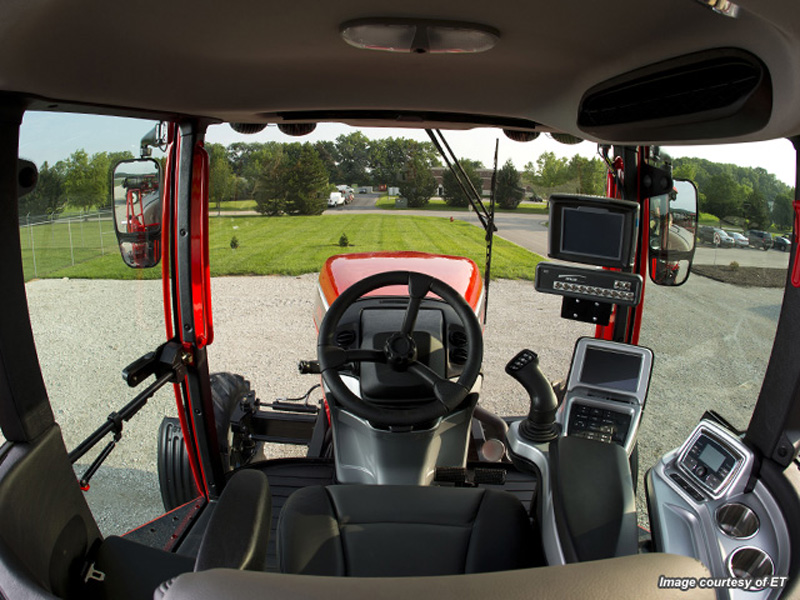
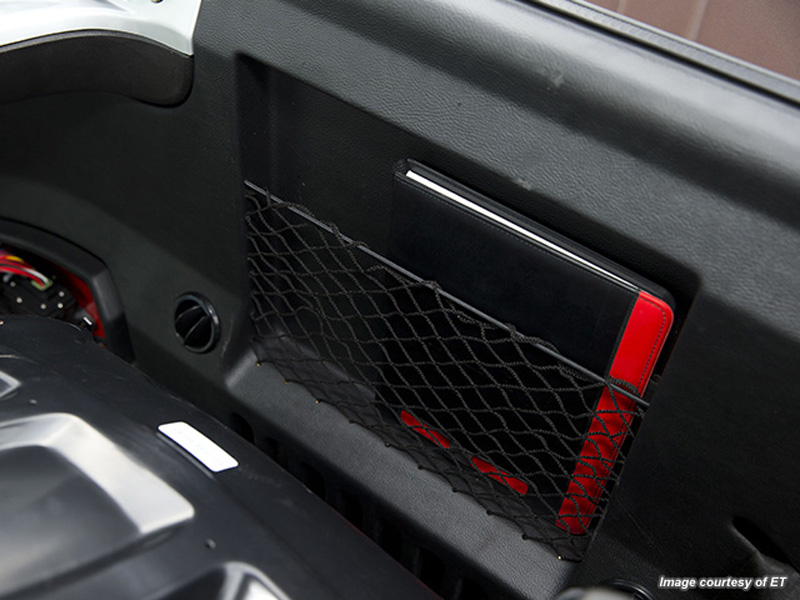
Material Versatility
Thermoforming is compatible with a wide range of thermoplastics, including ABS, PVC, Polyethylene, and more. This versatility enables the selection of materials based on specific properties like strength, flexibility, heat resistance, and cost, tailoring products to exact application needs.
High-Quality Finish
The process produces parts with excellent surface detail and consistency. Thermoformed components have smooth finishes and can incorporate textures or coatings, enhancing both the aesthetic appeal and functionality of the final product.
Scalability
Whether you need a small batch or a large production run, thermoforming is scalable to your production needs. Manufacturers can efficiently adjust production volumes without significant changes in tooling or processes.